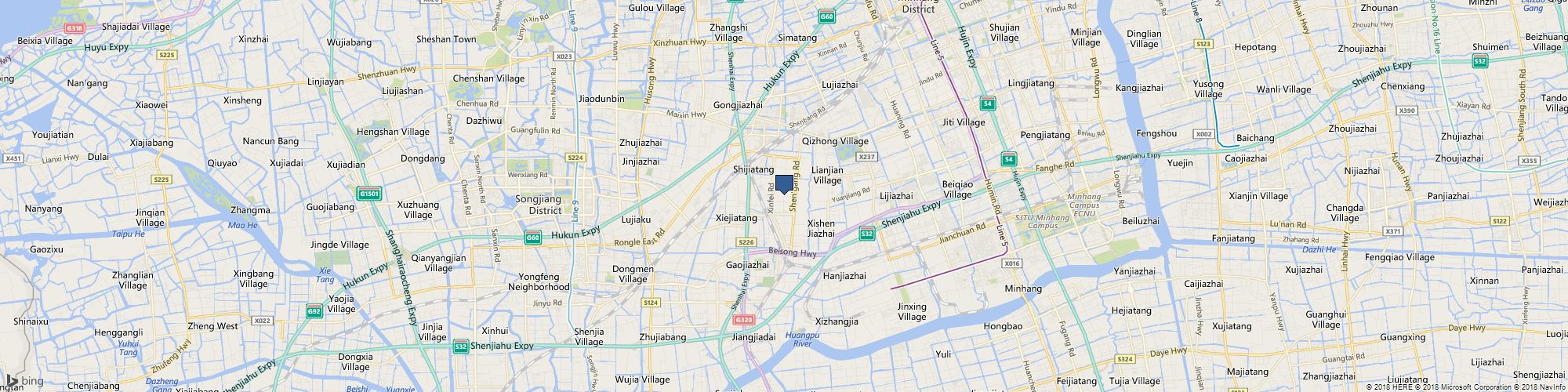
Variable Frequency Drives Manufacturer
A variable frequency drive controls alternating current torque and motor speed in electro-mechanical drive systems. In layman’s terms, it is an adjustable speed drive that regulates the frequency and voltage to the motor. You can find variable frequency drives, or VFDs, in everything from small appliances to giant compressors.
Variable Frequency Drives Manufacturer is a leader among variable frequency drive suppliers. Our company concentrates on VFD design and VFD manufacture. Variable Frequency Drives Manufacturer is an america VFDS Company located in Los angeles. Our main focus is creating the highest quality products. The main products single phase to three phase VFD, three Phases to three Phase VFD and so on.
For industrial purpose the power is to be delivered for larger distance hence AC power supply is required to drive the motors. The rectifier in a VFD is used to convert incoming ac power into direct current(dc) power. There are 3 pair of rectifier combination is used for converting 3 phase AC into DC Normally 6,12 or 18 diodes will be used to serve this purpose. Rectifiers can be built using diodes, silicon controlled rectifiers(SCR), or transistors to rectify power. After the power flows through the rectifiers it is stored on a dc bus. The dc bus contains capacitors to accept power from the rectifier and stores it and finally delivers that power through the inverter section.
Variable frequency drives can be used to control the speed of a machine. There can be significant energy reduction if the machine is slowed down when it does not need to operate at full speed. For example, pumps operated so that they run at a speed dependent on the flow requirements will reduce the cavitation losses in the pump. If the pump is required to run at constant full speed, the addition of a VFD will actually waste another 5% of energy.
Installing variable frequency drives (VFD) are one of the easiest ways to save a significant amount of the energy required to run fans and pumps. Most fan and pump devices are very inefficient when running at part-load conditions, so installing a VFD drastically reduces the energy consumed during those part-load periods. Over the typical life cycle, a VFD greatly reduces the total cost of operation.
All VFD applications require programming. You have to make it do what you want. Parameters like minimum and maximum frequencies, number of motor poles, maximum current, overload response, braking behavior, acceleration profiles, etc. must be set by the user to match your installation's needs. The voltage/frequency curve is user configurable too, which is very useful for your kind of application where you are operating outside the normal frequency range of the motor. Good VFDs come with a display that can be set to show the motor speed (or any number of other parameters). If I were doing this, I would use a 1HP 208V two-pole motor and a 1HP VFD with a 240V input.
Most any 3 phase input VFD unit built after 1996 is capable of operating on single phase input (be careful for the exceptions) with an appropriate "derating" of the drive. Rule of thumb - derate by 1/2. A 10HP VFD fed by single phase power will be suitable for running a 5HP 3 phase motor. Depends on the manufacture but most offer a Micro line and they are small over a wide HP range. I remember the first VFD I saw in 1976 had to be lifted with a fork truck and it was only 2HP. I have a 3HP unit I can easily hold in my hand and the packages will continue to get smaller I'm sure.
VFDs are used to replace three phase service when only single phase is available. But VFDs can do lots more than just get you three-phase. There are cases where you will need three phase input to a VFD but these are super advanced and I will not get into these here.